Resins are generally considered a family of substances that are viscous and convert into rigid polymers through a curing process. A resin can occur both naturally as well as synthetic – made in the labs, while many of the artificial can come close to their natural counterparts – a lot of them have very different properties.
Synthetic resins have several sources, classes, and end-uses. Few are manufactured by the esterification of organic compounds. The others are like thermosetting plastics, where the term resin can be considered for the reactant or the product. In the case of a copolymer, one of the monomers – apart from the resin – is called the hardener.
In this article, we look at various different types of resins, their properties, and their applications.
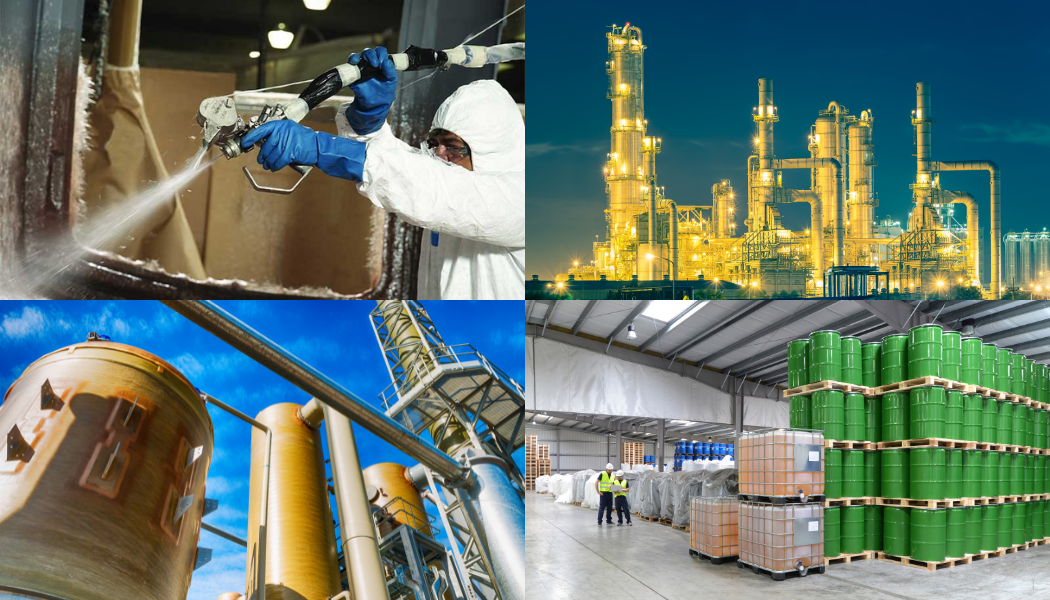
Polyester Resin
These types of resins are by the reaction of dibasic organic acids and polyhydric alcohols. They are known to be very flexible, show extreme resistance to heat, chemicals, and flame; while maintaining a low cost.
These polyester resins are popularly used in OEM components, coatings, construction, laminates, decorative accessories, etc.
Phenolic Resin
These types of thermosetting resins are quite durable, heat and impact resistant, and also show resistance to chemical corrosion and moisture penetration.
They are used for a plethora of products such as brake linings, electrical components, laminates, adhesive for concrete, mods, etc.
Alkyd Resin
Alkyd Resins are thermoplastic polyester resins that are made by heating polyhydric alcohol and polybasic acids. They demonstrate great electrical and thermal properties, as well as good chemical resistance.
They are extremely cost-effective and are used for electrical insulation, electronic components, paints, and putty fillers.
Polycarbonate Resin
Polycarbonate resins are thermoplastics that are developed from bisphenol A and phosgene. They possess a high refractive index, resistance to staining and filtration, as well as electrical and thermal dimensional stability.
They are used in applications such as metal replacements, safety helmets, lenses, photography film, electrical components, and insulators.
Polyamide Resin
Polyamide resins contain an amide group as a recurring part of their molecular chains. They are easily molded, strong and resistant, and lightweight. You can learn more about them here.
They have a low friction coefficient and are abrasion and chemical resistant. They are used for nonlubricated bearings, fibers, gears, sutures, tires, watchbands, packaging, and bottles.
Polyurethane Resin
Polyurethane resins are of the copolymer group which comprises polyol and isocyanate components. They exhibit great versatility when combined with other resins, as they have high film elasticity and substrates adhesion.
They additionally have a good balance of durability and toughness. They can be found in applications like insulation, elastomers, adhesives, and foam liners for clothing.
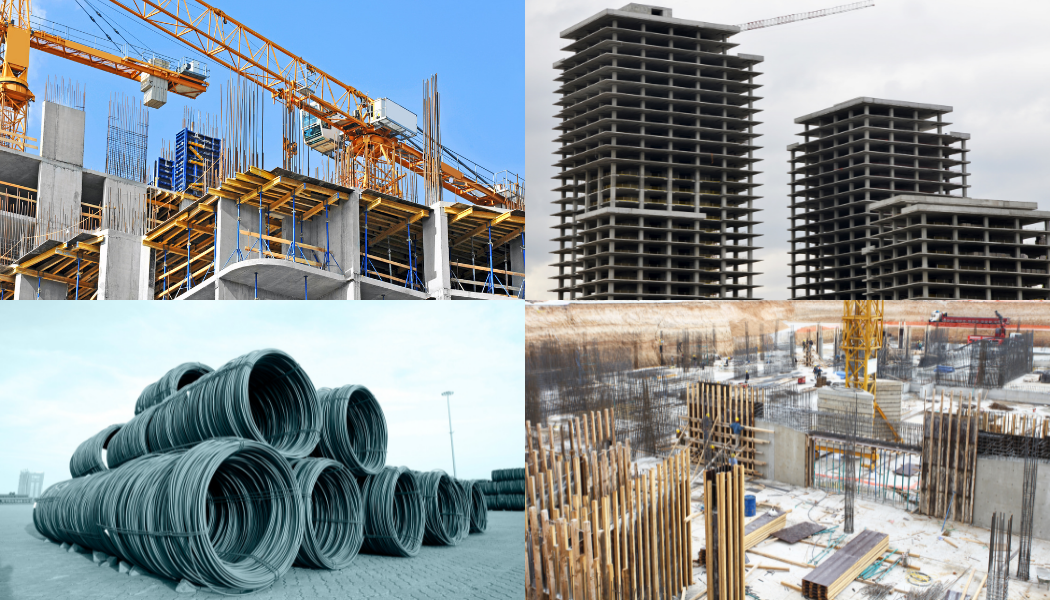
Silicone Resin
Silicone resins were previously made with sodium silicate and other chlorosilanes but are currently formulated with the less reactive tetraethoxysilane or ethyl polysilicate and several disiloxanes.
Resins of this kind possess great thermal and oxidative stability, along with flexibility and water-repelling qualities. Due to their 3D structure, they form hard films. These properties help them in their use for laminates, encapsulated resins, defoamers, and water-resistant applications.
Epoxy Resin
Epoxy resins aka polyepoxides are a type of reactive prepolymers and polymers which contain epoxide groups.
These resins have excellent chemical and heat resistance and strong adhesion properties. They are commonly used for laminates, adhesives, flooring, linings, propellers, and surface coatings.
Polyethylene Resin
Polyethylene resins are the most common kind of resin, with over 200 million tons produced every year. They have great steam and chemical resistance along with a high degree of flexibility.
They can be used for packaging for films and laminates, cable insulation, coatings, molds, linings, and pipes.
Acrylic Resins are of thermoplastic or thermosetting plastic substances created from acrylic acid, methacrylic acid, or other related compounds.
Acrylic products are transparent with good tensile strength, with additional impact and UV resistance benefits. They are used for panels, adhesives, elastomers, signs, coatings, and translucent tiles.
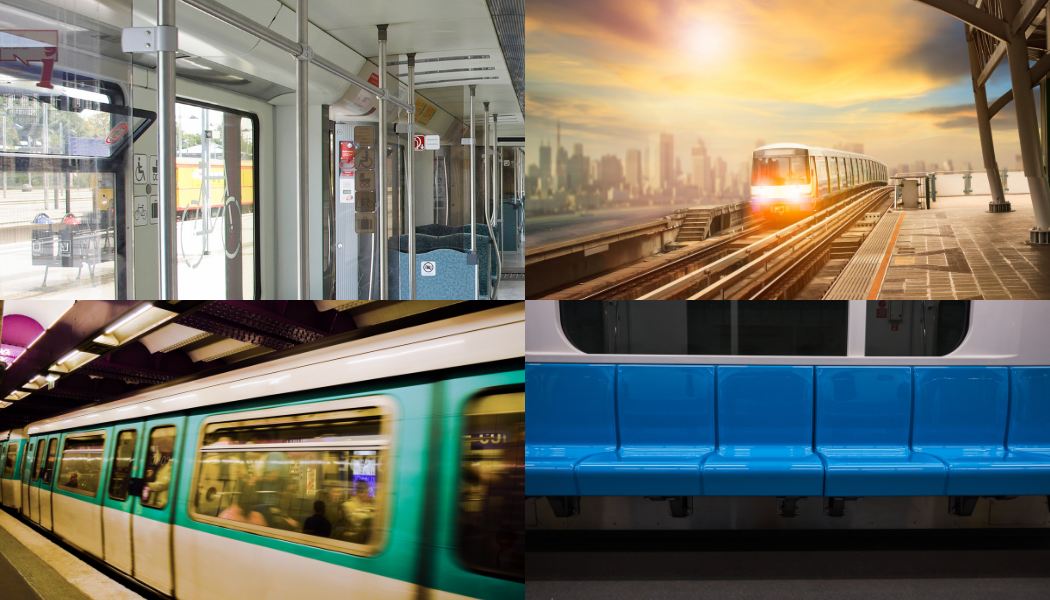
Polystyrene Resin
These resins are aromatic hydrocarbon polymers made from the monomer styrene. They are low-cost and easily produced, with excellent resistance to acids, alkalis, and salts.
They also have good clarity and flexibility. Their usages include insulation, pipes, cooling towers, rubber, automotive instruments, and dashboards
Polypropylene Resin
These resins are also a type of thermoplastic polymer resin that does not contain BPA. They are colorless with low density and exhibit great heat resistance. They can be sterilized, so they’re ideal for medical equipment.
Further, they have great chemical resistance. They are found in toys, electronic components, fibers and filaments, pipe and production tubing, and coatings.
The Resin Excellence
This article was a summary of all different and prevalent types of resins, if you wish to know more about these or obtain customized resin solutions for your company then kindly check out our products range. If you have any specific queries or want to reach out to us to know our capabilities – then click here.
This article presented an understanding of the different types of resins. For more information on related products, consult our other guides or visit the Thomas Supplier Discovery Platform to locate potential sources of supply or view details on specific products.
Contact Us
Website: www.crestresins.com
Phone: +91 9879233188
Email: enquiry@crestresins.com
Address: 605/A, 6th Floor, Tower D, Times Square Grand Office, Sindhubhavan Marg, Near Taj Hotel, Ahmedabad, Gujarat – 380059